Introduction
The Indian housing sector is on the brink of a technological revolution. Traditional construction methods, often plagued by high costs, labor shortages, and long timelines, are being challenged by an emerging innovation—3D-printed houses. This groundbreaking technology has the potential to reshape India’s architectural landscape, making homes more affordable, sustainable, and quickly built.
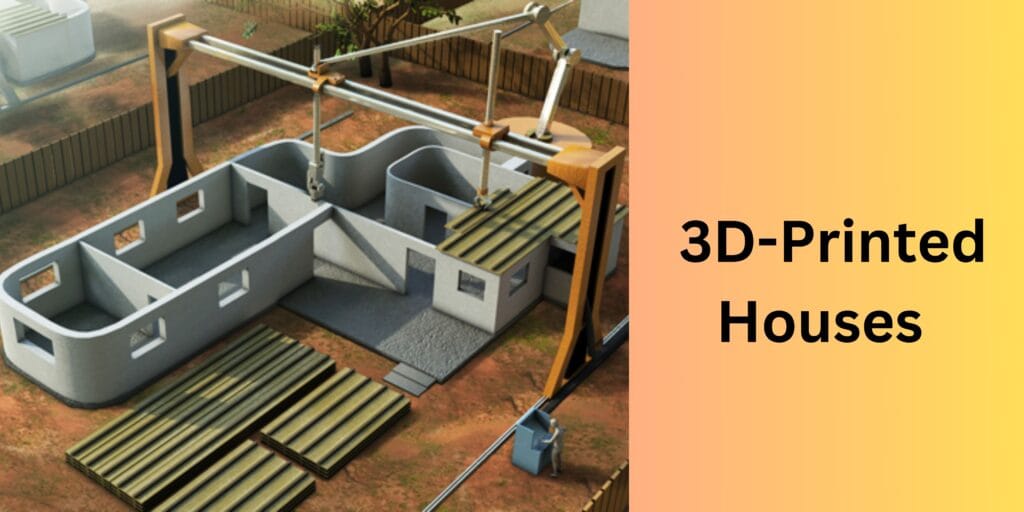
What is 3D-Printed Housing?
3D-printed housing involves using a large-scale 3D printer that extrudes a concrete-like material to create the structure of a building. Unlike conventional construction methods that require bricks, cement, and manual labor, 3D printing automates the process, reducing waste and increasing efficiency.
The technology uses specially designed concrete mixtures and is guided by a digital model to layer materials precisely. The result is a durable, cost-effective structure that can be completed in a fraction of the time compared to traditional methods.
Read more
Why is 3D-Printed Housing Gaining Popularity in India?
India is a country with a growing population and an ever-increasing demand for affordable housing. Traditional construction methods struggle to meet these demands efficiently. Here’s why 3D printing is catching attention in India:
- Speed of Construction – A 3D-printed house can be built within days, whereas traditional methods take months or even years.
- Cost Efficiency – Fewer materials and labor are needed, reducing overall costs.
- Eco-Friendliness – Less construction waste is produced, making it a sustainable choice.
- Customization – The technology allows for unique and intricate designs that would be difficult to achieve with traditional methods.
- Durability – 3D-printed houses use strong, weather-resistant materials that can withstand extreme conditions.
The Role of 3D Printing in India’s Housing Sector
Affordable Housing for the Masses
One of India’s most pressing issues is providing homes for low-income families. 3D-printed housing presents a solution by significantly lowering construction costs. With lower expenses on labor and materials, these homes can be made available at much more affordable rates.
Disaster-Resilient Homes
India faces natural calamities such as earthquakes, floods, and cyclones. Traditional homes often suffer severe damage, leading to displacement and loss. 3D-printed homes, designed with reinforced materials, can offer increased resistance to such disasters.
Faster Urban Development
With increasing urbanization, cities need more infrastructure in less time. 3D printing can rapidly build houses, schools, and hospitals, accelerating development projects in cities and rural areas.
Sustainable Construction
3D printing reduces material waste by using only the exact amount needed. The process is also energy-efficient, making it an environmentally friendly alternative to traditional construction.
Challenges Facing 3D-Printed Housing in India
Despite its advantages, the widespread adoption of 3D-printed homes in India faces some challenges:
- Regulatory Barriers – Indian construction regulations have not yet fully adapted to 3D printing technology.
- High Initial Investment – Setting up large-scale 3D printers requires significant capital.
- Material Availability – Specialized printing materials are not yet widely available in India.
- Skilled Workforce – While 3D printing reduces the need for labor, skilled technicians are required to operate and maintain the machinery.
Companies Leading the 3D-Printed Housing Revolution in India
Several startups and construction firms are exploring the potential of 3D-printed housing in India. Some notable names include:
- TVASTA Manufacturing – India’s first 3D-printed house was built by TVASTA in collaboration with the Indian Institute of Technology, Madras.
- L&T Construction – This major construction company is experimenting with 3D printing technology for housing projects.
- ICON & Habitat for Humanity – These international organizations are exploring partnerships to bring 3D-printed housing solutions to India.
FAQs
A: A 3D-printed house can be built in as little as 5-7 days, depending on the design and size.
A: Yes, they are made with strong, weather-resistant materials and can withstand natural calamities like earthquakes and cyclones.
A: The initial investment is high, but in the long run, 3D-printed houses are more cost-effective due to reduced labor and material costs.
A: Yes, 3D printing allows for greater design flexibility, enabling unique architectural features.
The Future of 3D-Printed Homes in India
The future looks promising for 3D-printed houses in India. As technology advances, costs will decrease, and regulatory frameworks will evolve. Government initiatives like Pradhan Mantri Awas Yojana (PMAY), which aims to provide affordable housing for all, could benefit greatly from integrating 3D printing technology.
Additionally, as the country moves towards sustainability, 3D printing’s eco-friendly nature will align with India’s goals for reducing carbon footprints in the construction sector.
Conclusion
3D-printed houses are no longer just a futuristic concept—they are a reality that is transforming India’s housing sector. With benefits like cost reduction, sustainability, and rapid construction, this technology has the potential to solve many of India’s housing challenges. While there are hurdles to overcome, the increasing interest from companies, the government, and investors indicates that 3D-printed homes will play a significant role in India’s architectural future.